La evolución de los terminales conductores y sensibles a la temperatura de latón niquelado
En el mundo de la fabricación de componentes electrónicos y eléctricos, la demanda de conectores de alto rendimiento está en constante evolución. Los terminales de latón niquelado, sensibles a la temperatura y conductores, son uno de estos componentes, cuya importancia ha ido en aumento en diversas industrias. Estos terminales se utilizan comúnmente en circuitos electrónicos, sistemas automotrices y aplicaciones de energías renovables, donde la confiabilidad, la conductividad y la resistencia a condiciones extremas son esenciales. El proceso de producción de estos terminales implica una selección avanzada de materiales, técnicas de fabricación complejas y un control de calidad para garantizar un rendimiento duradero.
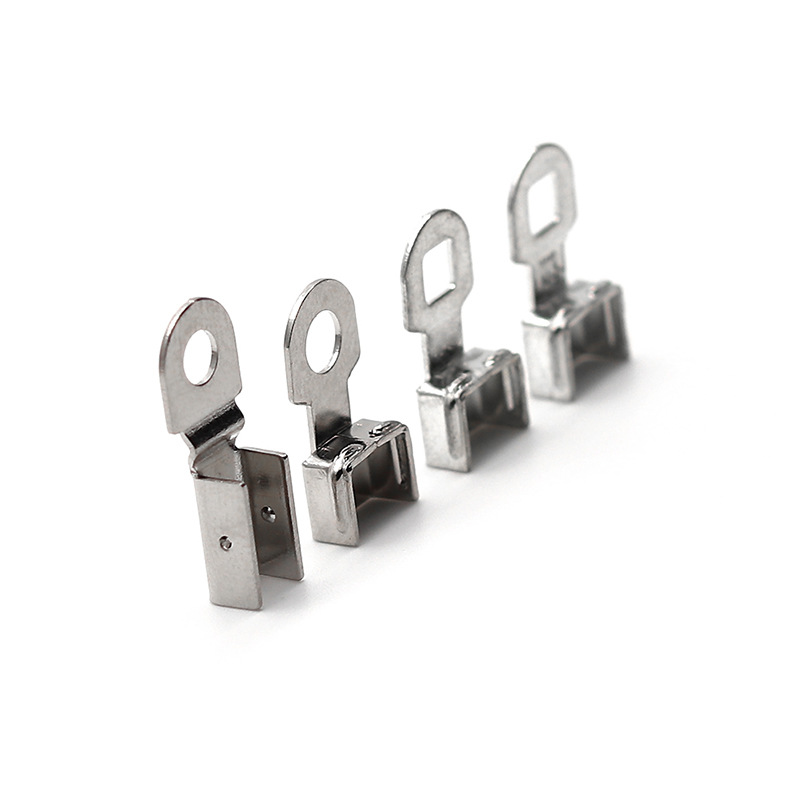
Composición y beneficios del material
El material base de la mayoría de los terminales conductores y sensibles a la temperatura es el latón, una aleación metálica compuesta principalmente de cobre y zinc. El latón se ha elegido desde hace mucho tiempo por su excelente resistencia, durabilidad y resistencia a la corrosión. Sin embargo, para aplicaciones que requieren mayor protección y mejor conductividad, se le aplica un recubrimiento niquelado. Este recubrimiento mejora la resistencia del terminal a la corrosión y la oxidación, y mantiene una conexión eléctrica estable incluso en entornos hostiles.
En una planta de producción, se decidió utilizar tereftalato de polietileno de baja densidad (LDPE) como recubrimiento, lo que mejoró tanto la flexibilidad como el rendimiento. La elección del niquelado se basó en su excelente capacidad para proteger el latón de la humedad y los contaminantes ambientales, a la vez que el latón proporcionaba la resistencia a la tracción y la estabilidad necesarias.
Esta combinación de materiales es especialmente valiosa en aplicaciones que requieren un alto nivel de conductividad eléctrica, como en dispositivos electrónicos, cableado automotriz y sistemas de almacenamiento de energía. El niquelado aumenta la conductividad del latón, previniendo la corrosión superficial que, de otro modo, podría reducir su rendimiento con el tiempo.
El proceso de fabricación
La producción de terminales de latón niquelado es un proceso meticuloso que consta de varias etapas para lograr los resultados deseados. La primera etapa consiste en obtener latón de alta calidad, que posteriormente se moldea para obtener la forma deseada. Se emplean técnicas de ingeniería de precisión para garantizar que los terminales cumplan con las más estrictas tolerancias de tamaño, forma y propiedades eléctricas.
Una fábrica utiliza una técnica conocida como galvanoplastia para aplicar el recubrimiento de níquel. El proceso consiste en sumergir el terminal de latón en un baño con sales de níquel y aplicar una corriente eléctrica para depositar una fina capa de níquel sobre la superficie del latón. El espesor de la capa de níquel es fundamental para garantizar una protección adecuada contra la corrosión, manteniendo al mismo tiempo una alta conductividad eléctrica. En una planta en Asia, por ejemplo, el proceso de niquelado se controla cuidadosamente para lograr un espesor de recubrimiento de 5 a 10 micras, lo que mejora significativamente el rendimiento y la durabilidad del terminal.
Tras el recubrimiento, los terminales se someten a un proceso de curado donde se aplica calor para solidificar el recubrimiento de níquel. Esto garantiza que el recubrimiento se adhiera correctamente al latón y ofrezca el nivel deseado de conductividad y resistencia térmica. En una fábrica norteamericana, el proceso de curado se optimiza para aumentar la productividad, lo que mejora la eficiencia de producción en un 15 % y reduce el consumo de energía.
Aplicaciones en diversas industrias
Las propiedades únicas de los terminales de latón niquelado los convierten en la opción ideal para diversas industrias. En el sector automotriz, por ejemplo, estos terminales se utilizan en sistemas eléctricos de alta tensión, como los de los vehículos eléctricos (VE). Su capacidad para mantener una conductividad estable a altas temperaturas y en condiciones ambientales adversas los hace especialmente adecuados para las conexiones de baterías eléctricas. Un fabricante de automóviles descubrió que el uso de terminales de latón niquelado en sus paquetes de baterías para VE contribuía a reducir la resistencia de contacto y a mejorar el rendimiento general del sistema eléctrico.
En el sector energético, estos terminales se utilizan a menudo en sistemas de paneles solares y convertidores de energía eólica, donde la fiabilidad es fundamental. Un fabricante de energías renovables observó que los terminales de latón niquelado eran especialmente eficaces para garantizar una conexión eléctrica estable a pesar de la exposición frecuente a condiciones climáticas extremas. Estos terminales mantienen su integridad a temperaturas de entre -40 °C y +120 °C, lo que garantiza una transmisión de energía constante y la eficiencia del sistema.
La electrónica es otra industria importante donde estos terminales son indispensables. Los fabricantes de teléfonos inteligentes, portátiles y otros dispositivos de alta tecnología confían en estos terminales por su capacidad para manejar altas corrientes y mantener un tamaño compacto. Una importante empresa de electrónica comenzó recientemente a utilizar terminales de latón niquelado en el ensamblaje de las pantallas de sus teléfonos móviles, argumentando su conductividad superior y su tamaño mínimo, esenciales para sus dispositivos delgados.
Resistencia ambiental y durabilidad
Una de las características más destacadas de los terminales de latón niquelado es su resistencia a la corrosión y la oxidación. Con el tiempo, la exposición a la humedad, el calor y otros factores ambientales puede causar la degradación de muchos metales. Sin embargo, el niquelado previene estos problemas al formar una barrera protectora sobre la superficie del latón. Esto hace que los terminales sean muy duraderos y aptos para su uso en exteriores e industriales.
En una instalación europea, los terminales se sometieron a rigurosas pruebas de niebla salina, simulando los efectos corrosivos de los entornos marinos. Los terminales de latón niquelado resistieron la exposición sin mostrar signos significativos de corrosión, lo que proporciona una fiabilidad a largo plazo. Este nivel de durabilidad es esencial en sectores como la automoción, donde las piezas se exponen frecuentemente a la sal de carretera y otros elementos corrosivos.
Además, la estabilidad térmica de estos terminales es impresionante. El niquelado garantiza que funcionen en condiciones extremas de temperatura sin comprometer su rendimiento. En el sector automotriz, por ejemplo, estos terminales se utilizan en unidades de control de motores, que suelen experimentar fluctuaciones rápidas de temperatura. Su capacidad para soportar altas y bajas temperaturas sin afectar la conductividad eléctrica los convierte en una opción confiable para estas aplicaciones.
Innovación en la fabricación
Ante la creciente demanda de componentes eléctricos de alto rendimiento, la fabricación de terminales de latón niquelado continúa evolucionando. En particular, se han introducido innovaciones destinadas a reducir los costes de material, manteniendo al mismo tiempo el rendimiento del producto. Algunos fabricantes han comenzado a experimentar con capas de niquelado más delgadas, optimizando así el proceso de galvanoplastia para utilizar menos material y, al mismo tiempo, ofrecer una protección adecuada.
En un caso, una fábrica en Latinoamérica introdujo una técnica avanzada de galvanoplastia que permitió un control más preciso del espesor del recubrimiento. Como resultado, la empresa logró reducir los costos de material en un 10% y mejorar el rendimiento eléctrico del terminal en un 15%. Esta innovación le ha permitido mantenerse competitiva en un mercado cada vez más sensible a los precios.
Además, los fabricantes también se centran en el desarrollo de terminales compatibles con sistemas inteligentes. En el futuro, estos terminales podrían incluir sensores para monitorizar la temperatura o la conductividad, lo que permitiría obtener información en tiempo real sobre su rendimiento. Esto podría ser especialmente útil en industrias como la electrónica y la automoción, donde la monitorización y la optimización del rendimiento son cruciales.
Tendencias del mercado y perspectivas futuras
El mercado de terminales termosensibles y conductores de latón niquelado continúa creciendo, impulsado por los avances en vehículos eléctricos, energías renovables y electrónica. Según informes del sector, se prevé que la demanda de terminales de alto rendimiento, solo en vehículos eléctricos, aumente un 30 % en los próximos cinco años. A medida que estas industrias se expandan, también lo hará la necesidad de conectores que mantengan altos niveles de conductividad y resistan los desafíos de las temperaturas y condiciones ambientales extremas.
Además, la preocupación por la sostenibilidad está impulsando a los fabricantes a buscar maneras de reducir el impacto ambiental de sus procesos de producción. Una fábrica adoptó recientemente técnicas de recubrimiento más eficientes energéticamente, lo que contribuyó a reducir su huella de carbono en un 20 %, a la vez que mejoró el rendimiento de las terminales.
El futuro de los terminales de latón niquelado se presenta prometedor, gracias a la continua innovación en tecnologías de recubrimiento, materiales y aplicaciones. A medida que las industrias demandan soluciones más fiables, rentables y respetuosas con el medio ambiente, la importancia de estos terminales en los sistemas eléctricos modernos seguirá creciendo.
Conclusión
La producción de terminales termosensibles y conductores de latón niquelado es un proceso altamente especializado que requiere precisión, materiales avanzados y un riguroso control de calidad. Estos terminales son un componente crucial en muchas industrias modernas, desde la automoción hasta la electrónica y las energías renovables, ofreciendo una conductividad, resistencia térmica y durabilidad superiores. Con las innovaciones constantes y la creciente demanda de componentes eléctricos de alto rendimiento, los terminales de latón niquelado seguirán desempeñando un papel vital en el futuro de los sistemas eléctricos a nivel mundial.