Los terminales de latón niquelado se están convirtiendo en la opción predilecta para las industrias que requieren conexiones eléctricas de alto rendimiento, duraderas y resistentes a la corrosión. Estos terminales se utilizan comúnmente en sectores que abarcan desde la automoción hasta la aeroespacial, y ofrecen ventajas significativas sobre sus homólogos sin niquelado. A medida que las tecnologías evolucionan y las industrias exigen mayor fiabilidad, el uso de los terminales de latón niquelado sigue creciendo.
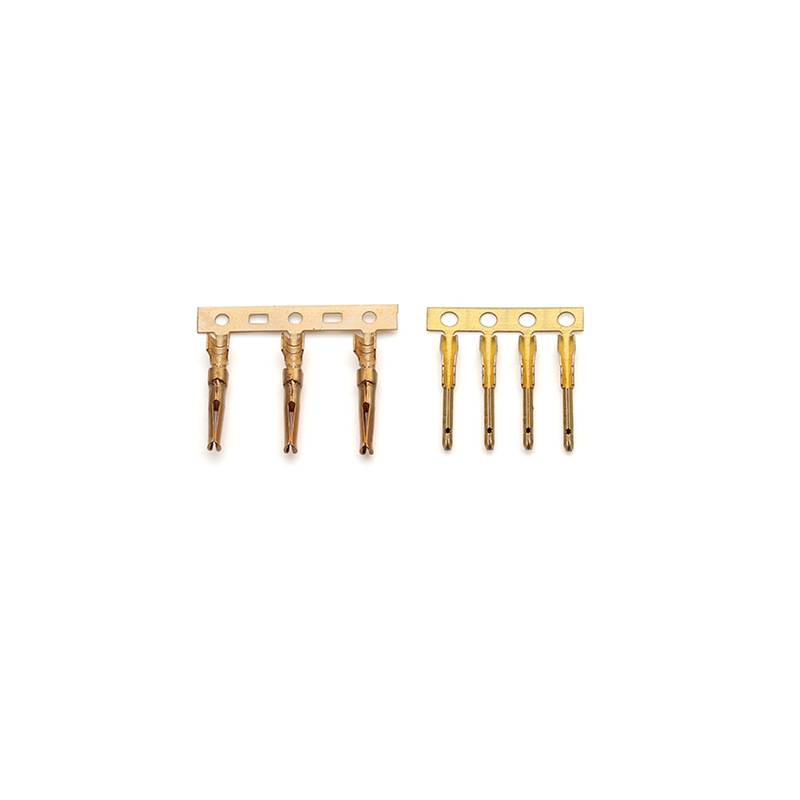
Una de las principales razones para usar terminales de latón niquelado es su excepcional resistencia a la corrosión. El niquelado proporciona una capa protectora que protege el latón subyacente de factores ambientales como la humedad, la sal y las temperaturas extremas. Esta característica es especialmente valiosa en aplicaciones automotrices e industriales. Por ejemplo, muchos fabricantes de automóviles, como Ford y Toyota, utilizan terminales de latón niquelado en el compartimento del motor y las conexiones de la batería. En estos entornos, donde el calor y la humedad suelen ser elevados, el recubrimiento de níquel previene la corrosión, asegurando que los terminales mantengan una conexión estable a lo largo del tiempo.
Los terminales de latón niquelado también se prefieren en industrias donde la conductividad eléctrica y la fiabilidad a largo plazo son cruciales. Si bien el latón tiene una conductividad menor que el cobre puro, el niquelado mejora el rendimiento general al mejorar la durabilidad y la resistencia a la oxidación del terminal. Esto garantiza que las conexiones eléctricas se mantengan estables, incluso en entornos con alta vibración. Un buen ejemplo de esto se puede observar en el sector aeroespacial, donde estos terminales se utilizan en los sistemas de cableado de aviones comerciales como el Boeing 787. Las duras condiciones de gran altitud y las variaciones de temperatura hacen que la corrosión sea un grave problema. Al utilizar terminales de latón niquelado, Boeing garantiza la durabilidad y fiabilidad de los sistemas eléctricos de la aeronave, reduciendo significativamente el riesgo de fallos.
The manufacturing process of these terminals also plays a crucial role in their effectiveness. Electroplating is the most common method for applying the nickel coating, providing a uniform and durable finish. The plating thickness is carefully controlled to balance performance and cost. Research from the Journal of Electrochemical Society highlights that nickel plating thicknesses between 5 and 10 microns can increase corrosion resistance by up to 30%. This makes the process cost-effective, as the added durability compensates for the slight increase in manufacturing costs—an important factor in industries where performance outweighs price.
Nickel plated brass terminals are also known for their mechanical properties. The nickel coating adds hardness to the brass, making these terminals more resistant to wear and tear. This is especially useful in applications where frequent connections and disconnections occur, such as in industrial automation or consumer electronics. Companies like Siemens have adopted nickel plated brass terminals in their automated control systems to ensure that their connectors withstand frequent use without deteriorating. Tests published in the Wear Journal show that nickel plated brass terminals exhibit 35% more resistance to wear than non-plated alternatives, making them ideal for high-frequency applications.
A medida que las preocupaciones ambientales cobran mayor relevancia, los terminales de latón niquelado también se fabrican teniendo en cuenta consideraciones ecológicas. Las empresas adoptan cada vez más métodos de niquelado sin cianuro para reducir el uso de sustancias químicas tóxicas. Heraeus, por ejemplo, ha sido pionera en tecnologías de galvanoplastia sin cianuro, lo que permite la producción de terminales de latón niquelado de alta calidad sin impactos ambientales perjudiciales. Este cambio se alinea con las normas regulatorias globales, como la directiva RoHS de la Unión Europea, que restringe el uso de ciertas sustancias peligrosas en equipos electrónicos.
The demand for nickel plated brass terminals is not confined to traditional industries. With the rise of electric vehicles (EVs), the need for robust, corrosion-resistant electrical components is more significant than ever. In electric vehicles, where the performance of electrical systems is crucial to the vehicle’s efficiency and safety, manufacturers like Tesla are turning to nickel plated brass terminals for their battery management systems and electric drivetrains. According to the Electric Vehicle Market Report, the demand for such terminals is expected to increase by more than 20% by 2025, as the EV market grows rapidly.
En conclusión, los terminales de latón niquelado ofrecen una combinación de durabilidad, resistencia a la corrosión y rendimiento eléctrico que los convierte en la mejor opción para diversas industrias. Desde la automoción y la aeroespacial hasta la automatización industrial y los vehículos eléctricos, estos terminales desempeñan un papel fundamental para garantizar la fiabilidad y la longevidad de los sistemas eléctricos. A medida que los métodos de producción evolucionan y las normas ambientales se vuelven más estrictas, el uso de terminales de latón niquelado seguirá expandiéndose, consolidando su lugar en el futuro de la tecnología.